<-- Resume
EV Clutch project
(E.I.T.)
Function Statement A device must successfully deliver unidirectional power to the electrical vehicle.
​
Requirements
-
The clutch system must not wear out before 1 million cycles.
-
The clutch must have a high enough torque rating to run with the electric motor.
-
The clutch system must provide enough torque to accelerate at a desirable rate (goal acceleration value to be determined).
​
Engineering Merit This project gives those involved the opportunity to decipher which kind of clutch system to use with the certain kind of car being worked on. The project can allow those involved to design a new clutch system. Cars are anticipated to be around for awhile and continual improvement in fuel efficiency, safety, and performance of cars is much needed; this project allows the opportunity to improve the vehicle. The project also allows those involved to gain experience in choosing optimal designs.
Calculations and analysis are needed to successfully complete the project to determine aspects such as torque, wear, power, inertia, acceleration, deflection and other quantified values. The engineer will get more practice at determining if the design will work with analyses.
​
Scope of Effort The goal is to successfully mount the clutch system in the electric vehicle to allow forward motion and allow the vehicle to coast (wheels spin freely) when the clutch is disengaged.
​
Success Criteria When all of the requirements have been met reliably, the project is a success.
​
MISSION:
Increase the fuel efficiency of the electric vehicle and help the CWU EV Club get the best Electrathon score to date.
Construction:

The clutch bearing slip fits onto the driving shaft on the electric vehicle (completed Jan. 17). The hub will be FN1 press fitted around the clutch bearing and all fastened to the sprocket with six #10-32 threaded screws.
The driving shaft and components must be disassembled to replace the collar with the clutch bearing where the collar was. A manual press was used to remove the collar in exchange for the clutch bearing.
A manual press will be used to perform the press fit between the hub and the clutch bearing. The inner diameter of the hub must be .9982 to .9993 inches for a proper FN1 press fit with the clutch bearing. The bolt circle diameter must be within 3 thousands of an inch from 1.75 inches to allow the screws to go through the hub and sprocket bolt holes simultaneously.
The hub will be manufactured using a CAD/CAM mill process (Completed Code Jan 31). Hub manufactured on Feb 7th with hub/clutch/screw assembly on the shaft completed the same day the hub is completely manufactured.
Click icon below for Project Report
Description Without a clutch, the electric vehicle has no device to allow for coasting when the pedal has been depressed. Engineering in this case can help to make sure the clutch system is efficient, reliable, and safe with design and analysis.
​
Motivation This project is a subproject for the Electric Vehicle (EV) club. The EV club has lost ground in recent years and making progress on the vehicles including the clutch and other devices could help the EV club get funding to continue as an entity.
​
​

Marquee Analysis

Description Without a clutch, the electric vehicle has no device to allow for coasting when the pedal has been depressed. Engineering in this case can help to make sure the clutch system is efficient, reliable, and safe with design and analysis.
​
Motivation This project is a subproject for the Electric Vehicle (EV) club. The EV club has lost ground in recent years and making progress on the vehicles including the clutch and other devices could help the EV club get funding to continue as an entity.
Reference: UC Berkeley
Related Requirement:
The clutch's torque rating must be higher than the calculated motor torque. **The clutch is rated at 17 lb-ft, which is higher than the motor torque 8.5 lb-ft (or 101 lb-in).** The design was limited to a 3/4 inch inner diameter clutch bearing. If a standard clutch was not strong enough, than a special material like titanium would've been considered and analyzed.
Other Analyses are in the Report file in Appendix A. Analyses include, Torque for Acceleration, Motor Power, Shear, Min. Diameter, Load, & Rx forces.
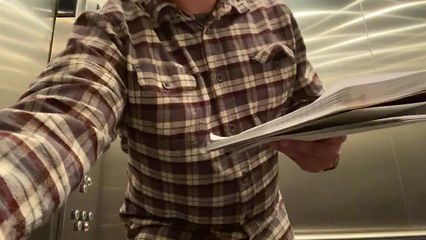
ELEVATOR PITCH
Construction images:
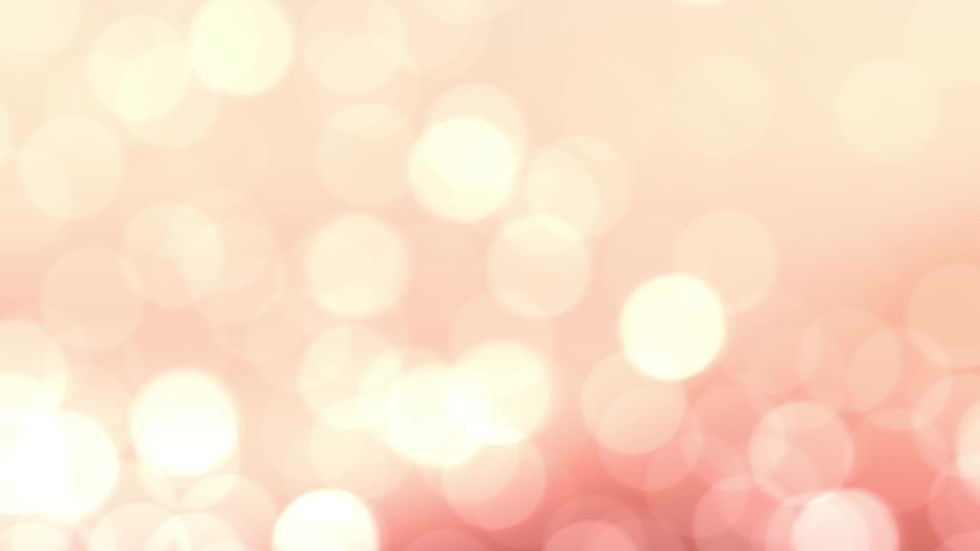


Six of these #10-32 threaded stainless-steel screws were needed to fasten the hub and clutch components in place against the sprocket. This is the third of three total parts this project requires.

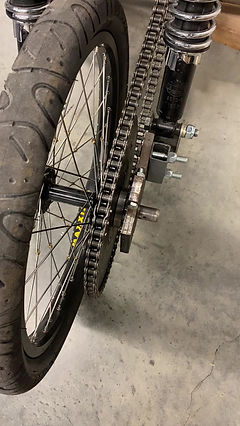
This is the assembly of all three components that are needed to make the clutch properly do what the design intended.
​
Check out the 1 minute video below to gain a quick visualization of the construction process:
Mating Holes Issue:
Between the holes on the hub, the holes on the sprocket, and the threaded holes by the wheel, there was enough misalignment to cause the clutch bearing to seize on the rear wheel shaft.
The holes on the hub were progressively drilled larger and larger until the clutch was no longer seizing, but allowing the said shaft to spin freely.

This stock was the second part purchased. This stock was used to manufacture the quick disconnect hub. A bandsaw cut the stock to be as wide as the hub's face width. A couple lathe operations reduced the face and created the bore hole where the clutch bearing was pressed into. A CAD/CAM program was created to drill the six bolt circle holes where the threaded screws pass through.
This is the purchased 3/4" ID one-way clutch bearing, the first ordered part.
A Gantt chart keeps track and lays out when necessary tasks for the project are expected to begin and be completed by.

This is the budget for the material it takes to complete the project. This is truly the amount of money that came out of pocket.
Estimated costs including labor and consulting are discussed in the budget and scheduling section of the project report.
An additional $211.00 was used to get better internet connection at the off campus site this project is working from. These costs would not have been issued if there was no pandemic.
Schedule:

Budget:
Clutch’s Affect on MPG:
-
Race the EV with clutch until battery is drained. Record MPG for run.
-
Race the EV w/o clutch until battery is drained. Record MPG for run.
-
Compare MPG with clutch vs. w/o clutch.
Improved Coasting Test on Hill:
*Use same person to steer car every time (same weight).
*Use a straight line path to minimize steering and side loads.
*Bring an allen wrench for attaching/removing the clutch system.
1. Mark a starting point on the hill and set all the tires pressure to 50 psi.
2. Line up the front of the car even with the starting point.
3. Let go of the car (don’t push) and let the vehicle coast until it stops without the aid of braking.
4. Mark off where the front of the vehicle stops coasting. Use one color for clutch trials and use a different color for trials without the clutch.
5. Repeat steps 2-4 until three or more trials are completed with the clutch on and clutch off.
Coasting Test Setup:
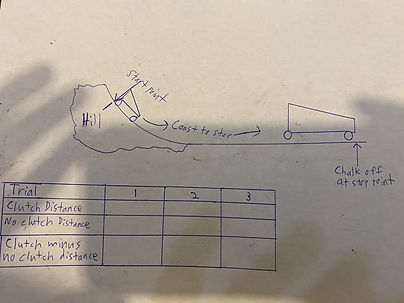
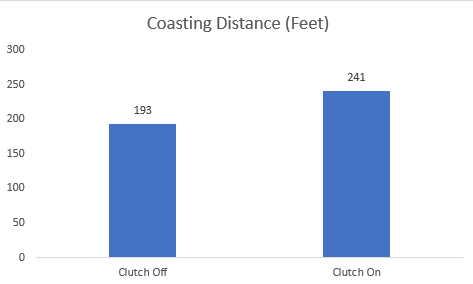
Unfortunately, the project is unknown to be a success since physical testing wasn't completed. This graph is just a baseline for when testing can be completed. If the real life "clutch on" coasting distance is shorter than the "clutch off" coasting distance, then the hub and clutch fit will need to be loosened.
The graphed results are only anticipated results using conservation of energy principles. Resources were not available for this time consuming test due to the pandemic and the student having to stay off campus, thus the student could not work with the clutch and vehicle.
The original test called for 10 yard pushes to get the coasting distance. The same force cannot be expected from each push, so it would cause a lot of issues with the results. A hill in the student's hometown which transitions into level ground inspired the improvement of the coasting test. Starting from the same reference height/point on the hill will result in constant speed and force each trial; making results much more reliable.